Design for Additive Manufacturing: Revolutionizing Industries
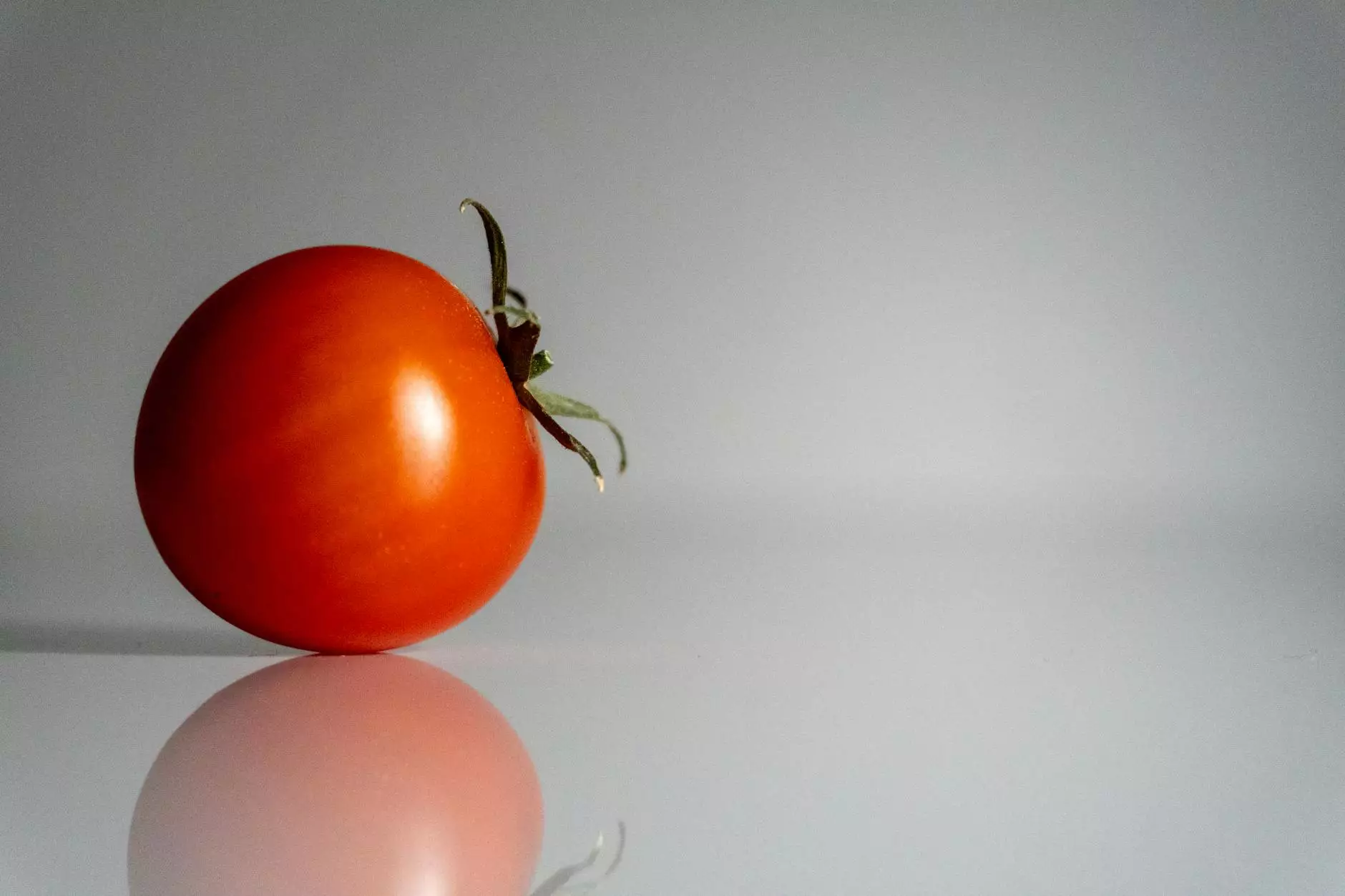
Design for additive manufacturing (DfAM) has emerged as a transformative approach in the realm of manufacturing. As industries strive to enhance efficiency, reduce waste, and innovate new products, DfAM stands as a crucial methodology that integrates design principles with the capabilities of additive manufacturing (AM). This article delves deep into the principles, applications, and benefits of DfAM, revealing how it is shaping the future of various sectors.
Understanding Additive Manufacturing
Additive manufacturing, commonly known as 3D printing, is a process of creating objects layer by layer from a digital model. Unlike traditional subtractive manufacturing, which involves cutting away material from a solid block, DfAM allows for the construction of complex geometries that are often unachievable with conventional methods. This technology can use a variety of materials, including plastics, metals, ceramics, and even biological tissues.
The Importance of Design in Additive Manufacturing
Effective design for additive manufacturing significantly influences the performance, cost-efficiency, and manufacturability of products. Recognizing that AM operates under different principles compared to traditional manufacturing methods, designers must adapt their workflows to take full advantage of the unique capabilities offered by additive technologies.
Key Principles of Design for Additive Manufacturing
- Material Efficiency: AM allows designers to minimize material usage, thereby reducing waste. Parts can be designed with intricate lattice structures that maintain strength while using less material.
- Complex Geometries: One of the standout features of DfAM is the ability to create complex shapes that would be difficult or impossible using traditional manufacturing methods.
- Integration of Components: DfAM encourages the consolidation of multiple parts into a single design, reducing assembly time and potential failure points.
- Customization: Due to the flexibility of 3D printing, products can be easily tailored to meet specific customer requirements, enhancing satisfaction and marketability.
Applications of Design for Additive Manufacturing
The applications of DfAM span across various sectors, demonstrating its versatility and efficacy. Here are some pivotal industries where DfAM is making a difference:
Aerospace Industry
The aerospace sector benefits significantly from DfAM due to the industry's demand for lightweight and high-strength components. By utilizing AM technologies, manufacturers are able to create parts such as:
- Fuel Brackets: Lightweight brackets that reduce overall aircraft weight.
- Engine Components: Complex designs that optimize airflow and combustion efficiency.
- Customized Tools: Specialized tooling required for specific applications that are both lighter and more efficient.
Medical Applications
In the medical field, DfAM has opened doors to personalized healthcare solutions, including:
- Prosthetics: Custom-fitted prosthetic limbs designed using patient-specific data.
- Bioprinting: The development of tissues and organs for transplants using additive techniques.
- Surgical Instruments: Tailored tools that enhance surgeon efficiency and precision.
Automotive Sector
Automotive manufacturers are leveraging DfAM to innovate and streamline production processes, such as:
- Prototyping: Rapid prototyping allows for quick iterations and design adjustments.
- Lightweighting Parts: Reducing vehicle weight to improve fuel efficiency.
- Customized Components: Addressing specific consumer needs, enhancing user experience.
Benefits of Design for Additive Manufacturing
The transition to DfAM is not only about technological innovation; it also brings substantial benefits that can significantly impact businesses:
Cost Reduction
By optimizing designs for AM, companies can reduce material costs, lower energy consumption, and minimize waste—leading to significant cost savings. Furthermore, the reduction in component count correlates directly with lower assembly costs.
Increased Speed to Market
The ability to rapidly iterate designs and produce parts on demand accelerates the time from concept to market. This agility allows companies to respond more quickly to changing consumer preferences or market conditions.
Enhanced Performance
Products designed with DfAM often exhibit superior performance characteristics due to optimized geometries that traditional manufacturing cannot achieve. This leads to innovations that outperform competitors’ offerings.
Sustainability
Utilizing design for additive manufacturing principles promotes sustainable practices by significantly reducing material waste and energy consumption associated with traditional manufacturing processes. This shift is vital as industries increasingly prioritize environmental responsibility.
Challenges to Implementing Design for Additive Manufacturing
Despite the numerous advantages, there are challenges associated with implementing DfAM:
Design Complexity
The intricate designs possible with AM can be a double-edged sword. Designers must have a thorough understanding of AM capabilities and limitations to ensure manufacturability while maintaining design integrity.
Material Limitations
While AM supports a broad range of materials, not all materials are suitable for every application. Identifying the right material that meets aesthetic and functional requirements can be challenging.
Regulatory Hurdles
Particularly in regulated industries (like aerospace and medical), obtaining certification for new AM-designed parts can delay implementation and add additional costs.
The Future of Design for Additive Manufacturing
The future of design for additive manufacturing appears promising, with ongoing advancements in technology and materials. The integration of AI and machine learning with AM is anticipated to optimize design processes further, enabling even greater innovation.
Moreover, as more industries adopt DfAM principles, collaborative efforts between design engineers, material scientists, and machine vendors will lead to enhanced workflows that prioritize efficiency and creativity.
Conclusion
Design for additive manufacturing is not just a trend but a fundamental shift in how products are conceived, designed, and produced. By embracing the principles of DfAM, industries can unlock a myriad of opportunities that result in superior products, cost savings, and sustainable practices. As this paradigm continues to evolve, the potential for innovation across sectors is boundless, making DfAM an integral part of the future of manufacturing.
Businesses looking to thrive in this new landscape should prioritize investments in DfAM training, capabilities, and technologies. The advantages are clear: those who adapt will not only survive but thrive in the rapidly changing world of manufacturing.