Understanding Plastic Injection Moulding Services: A Comprehensive Guide
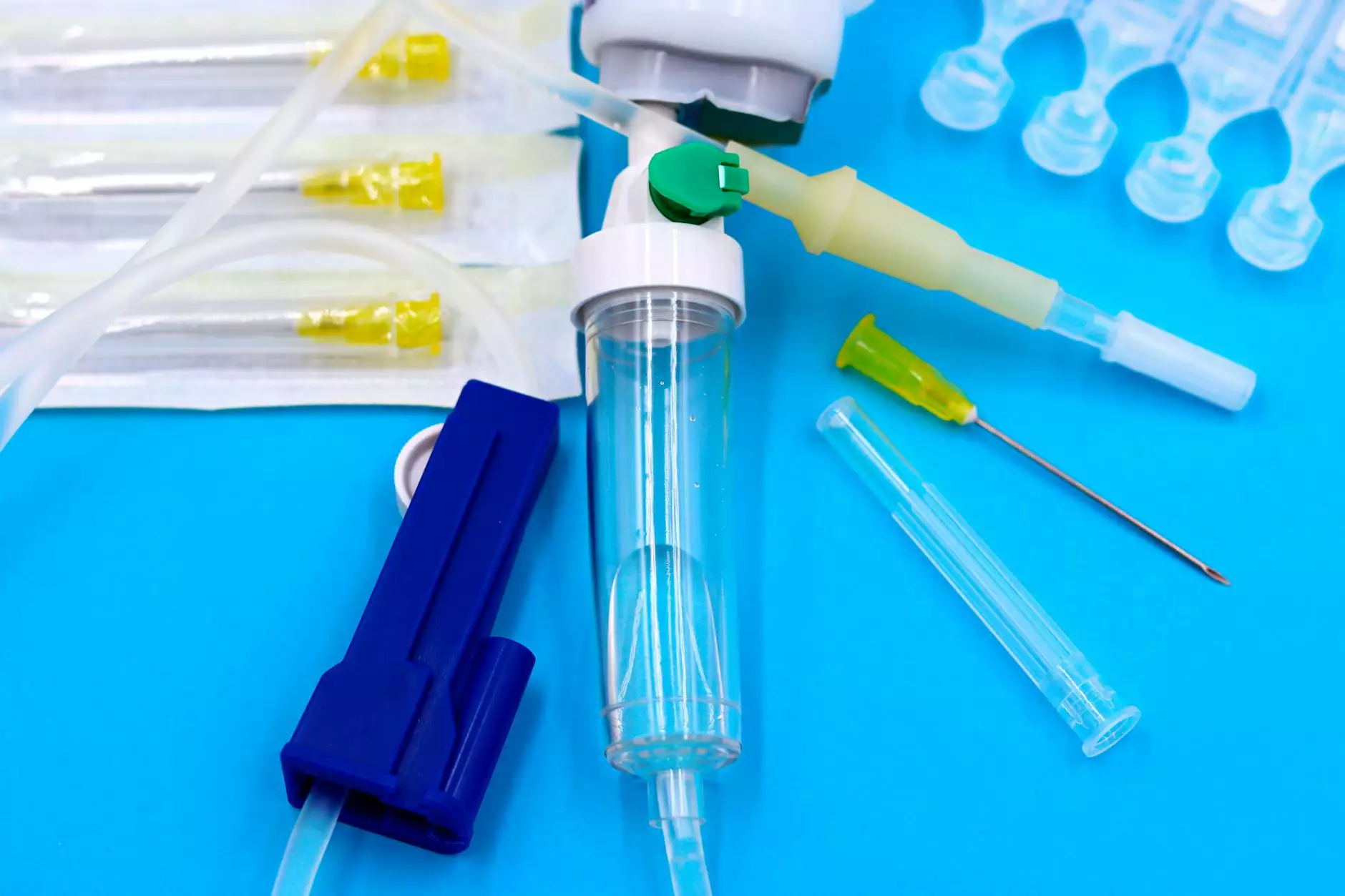
The manufacturing landscape is continuously evolving, and businesses are continually seeking efficient, cost-effective methods to produce high-quality components. Among these methods, plastic injection moulding service stands out as a pivotal process that facilitates precision engineering with a myriad of applications across various industries. This article delves into the intricacies of plastic injection moulding services, detailing its processes, advantages, applications, and its relationship with other production methods like machining, laser cutting, welding, and vulcanized industrial supplies.
What is Plastic Injection Moulding?
Plastic injection moulding is a manufacturing process used to produce parts by injecting molten material into a mould. It is widely utilized not only for its efficiency but also for its ability to produce high volumes of consistent, high-quality parts. The process involves several key stages:
- Clamping: Moulds are secured in a closed position under pressure.
- Injection: Molten plastic is injected into the mould cavity.
- Cooling: The plastic cools and solidifies to take the shape of the mould.
- Demoulding: The mould is opened, and the finished part is ejected.
Benefits of Plastic Injection Moulding Services
The choice of plastic injection moulding service offers an array of advantages that set it apart from other manufacturing techniques. Here are some of the most notable benefits:
- High Efficiency: Once the mould is created, the injection process can produce thousands of identical parts quickly, saving time and reducing labor costs.
- Cost-Effectiveness: The ability to mass-produce items means cost savings per unit, significantly lowering production expenses.
- Design Flexibility: Complex shapes and geometries can be achieved that would be difficult or impossible with other manufacturing methods.
- Material Versatility: A wide range of thermoplastics can be used, allowing manufacturers to select materials that are best suited for specific applications.
- Reduced Waste: The process generates minimal waste since excess material can often be reused in subsequent cycles.
Applications of Plastic Injection Moulding
Plastic injection moulding is used in numerous industries, proving its versatility and reliability. Here are some key sectors where this technology shines:
- Automotive: Used for manufacturing parts like dashboards, door panels, and other interior and exterior components.
- Consumer Goods: Applicably for a vast range of products, from toys to household items.
- Medical Devices: Ensuring precision and compliance with regulations, essential for components such as syringes, surgical tools, and other medical equipment.
- Electronics: Creating enclosures, connectors, and other components that protect sensitive electronics.
Plastic Injection Moulding vs. Other Manufacturing Processes
While plastic injection moulding is a powerful tool in manufacturing, it interacts closely with other processes such as machining, laser cutting, welding, and vulcanization. Here's how plastic injection moulding compares:
Machining
Machining is often used for producing precise components with tight tolerances. While machining is excellent for low-volume production or custom parts, plastic injection moulding services are superior for high-volume needs due to lower per-unit costs and faster production rates.
Laser Cutting
Laser cutting is a technique best suited for thin materials, allowing for intricate designs and clean cuts. In contrast, plastic injection moulding creates solid, three-dimensional objects with great detail, making it ideal for creating robust parts.
Welding
Welding is essential for joining materials, especially metals, and is less applicable for plastics. Where welding offers strength in joining components, plastic injection moulding excels at producing entire components in a single process.
Vulcanized Industrial Supplies
Vulcanization is a process primarily related to rubber materials. While both processes involve molding, plastic injection moulding caters specifically to plastic materials and offers greater flexibility in design and production.
The Future of Plastic Injection Moulding Services
As industries evolve, the landscape of manufacturing is also changing with innovative technologies like Industry 4.0, which combines automation, data exchange, and advanced manufacturing technologies. Here’s what to expect for the future of plastic injection moulding services:
- Enhanced Automation: Increased automation in manufacturing processes will enhance productivity, reduce labor costs, and minimize human error.
- Sustainable Practices: The push towards sustainability will lead to the development of more eco-friendly materials and processes in injection moulding.
- 3D Printing Integration: The combination of 3D printing with injection moulding can provide rapid prototyping capabilities alongside mass production.
- Customization: As consumer demand for personalized products grows, the ability to produce custom moulds for niche markets will be crucial.
Conclusion
In conclusion, plastic injection moulding service plays a vital role in today’s manufacturing sector, providing a multitude of advantages from high efficiency to design flexibility. Its applications span across industries, creating products that form the backbone of our daily lives and technological advancements. As businesses like Sumiparts continue to integrate more advanced technology and sustainable practices, the relevance and impact of plastic injection moulding will only grow. Embracing this technology gives companies the edge they need to meet the demands of an ever-evolving marketplace.