The Art and Science of Injection Plastic Molding
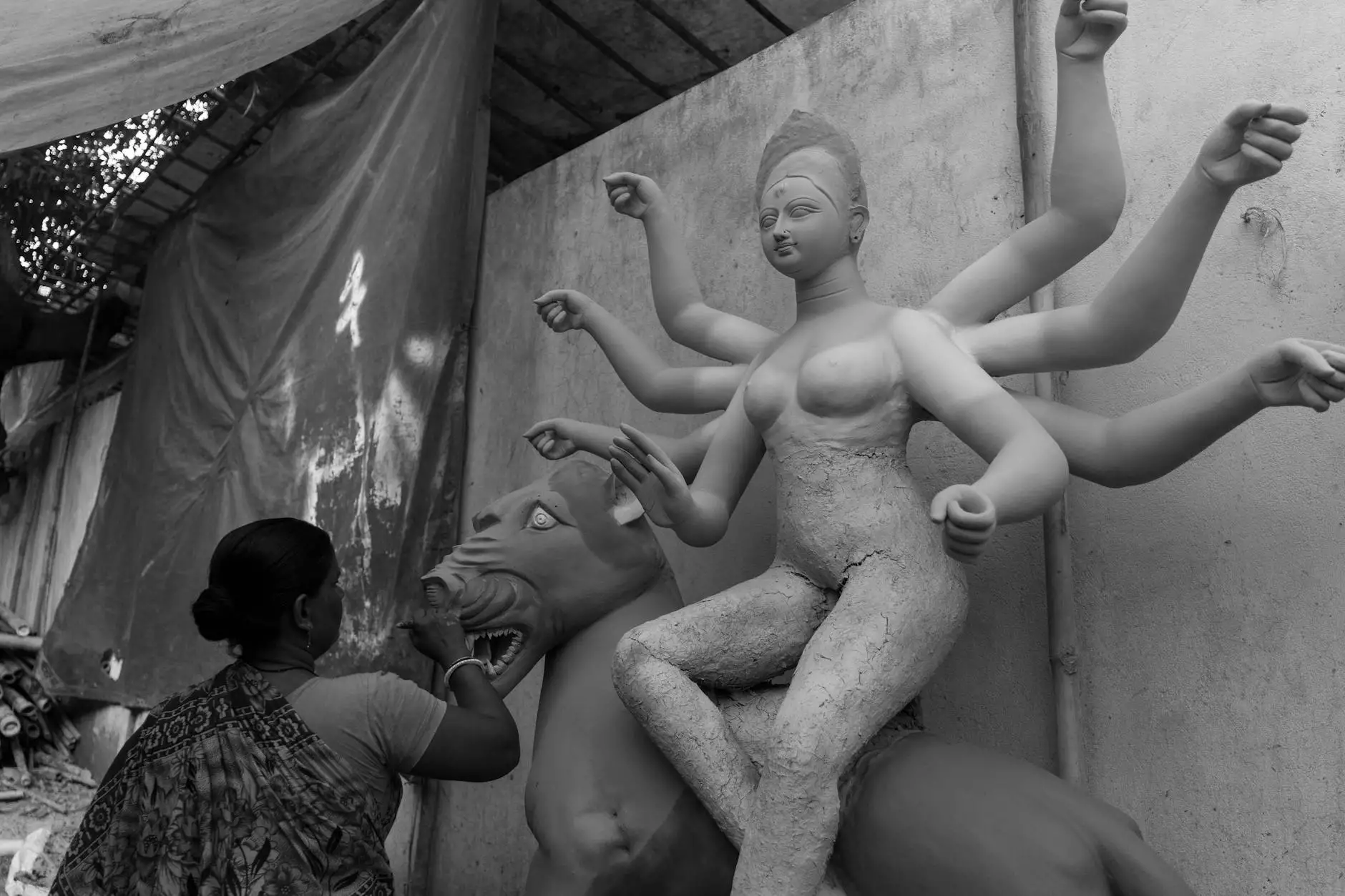
The injection plastic mold process is a key player in the manufacturing industry, particularly within the realm of metal fabrication and product development. This article aims to delve into the numerous aspects of injection plastic molding, including its definition, applications, advantages, and the best practices for leveraging this innovative technology for business growth.
Understanding Injection Plastic Molding
Injection molding is a manufacturing process used to make parts by injecting molten material into a mold. It is predominantly used for molding plastics, but metals, glasses, and other materials can also be utilized. This method is favored for high-volume production runs due to its speed and efficiency.
What is Injection Plastic Molding?
At its core, the injection plastic mold process begins with the creation of a mold—a hollow metal cavity that defines the shape of the finished product. Once the mold is prepared, plastic pellets are heated and injected into the mold under high pressure. Once cooled, the mold is opened, and the newly formed plastic part is ejected. This cycle can be repeated rapidly, making it a cost-effective choice for producing large quantities of identical items.
The Components of Injection Molding
Injection molding involves several critical components, including:
- Injection Unit: This component melts the plastic and injects it into the mold.
- Mold: A hollow form that shapes the plastic as it solidifies.
- Clamping Unit: This secures the mold during the injection process to withstand the high pressure.
- Control System: Automates the process, allowing for precision and reliability in production.
Applications of Injection Plastic Mold
The versatility of the injection plastic mold process allows it to be used across various industries. Here are some of the key areas where injection molding shines:
1. Automotive Industry
Injection molded plastic parts are extensively used in the automotive sector. Examples include dashboard components, interior trims, and various functional parts. The durability and lightweight properties of injected plastics contribute significantly to the efficiency of modern vehicles.
2. Consumer Goods
From toys to household appliances, many consumer goods are manufactured using injection molding. The ability to produce complex shapes efficiently makes it ideal for creating products that capture consumer interest and fulfill functional needs.
3. Medical Devices
The medical field relies heavily on injection-molded components for devices such as syringes, surgical instruments, and diagnostic equipment. The precision offered by this manufacturing method is paramount for ensuring safety and effectiveness in medical applications.
4. Electronics
Injection molding is crucial in producing casings, components, and various internal parts for consumer electronics. The combination of resilience and design flexibility allows manufacturers to create aesthetically pleasing and functional electronic devices.
Advantages of Injection Plastic Molding
Choosing injection molding for manufacturing offers numerous advantages, making it a preferred manufacturing method worldwide.
1. High Efficiency and Speed
Injection molding is renowned for its ability to produce parts quickly. With the potential for thousands of units to be produced daily, the method supports high-volume production requirements. This efficiency translates to reduced labor costs and faster time-to-market for products.
2. Design Versatility
One of the standout features of injection molding is its capacity for complex shapes and designs. Manufacturers can create intricate components that would be nearly impossible to achieve with other methods, thus enhancing product functionality and aesthetic appeal.
3. Material Efficiency
Injection molding minimizes waste during the production process. Excess material can often be recycled and reused, which not only conserves resources but also contributes to lower costs.
4. Consistency and Quality Control
In injection molding, the precision of the equipment ensures that each part produced is nearly identical. This consistency makes quality control easier and fosters a trustworthy relationship with customers who expect uniformity in products.
How Metal Fabricators Can Benefit from Injection Plastic Molding
For metal fabricators looking to expand their offerings, incorporating injection plastic mold processes can lead to significant benefits. Here’s how:
1. Diversification of Product Line
By adding injection molding capabilities, metal fabricators can broaden their product lines beyond traditional metal components. This diversification allows companies to tap into new markets and meet a wider array of customer needs.
2. Improved Customer Solutions
Combining metal and plastic parts can lead to innovative product solutions. For instance, a hybrid product that uses both materials can enhance functionality and performance, appealing to clients requiring advanced engineering solutions.
3. Cost-Effective Solutions
Integrating injection molding into operations can reduce manufacturing costs through efficient material usage and faster production cycles. This financial benefit is crucial for remaining competitive in the evolving manufacturing landscape.
4. Enhanced Product Development Capabilities
Having a comprehensive manufacturing capability that includes both metal fabrication and injection molding can streamline product development processes. Rapid prototyping and testing can lead to quicker turnarounds and greater innovation.
Best Practices for Successful Injection Molding
For businesses considering injection molding, adhering to best practices can maximize outcomes:
1. Choose the Right Materials
The choice of material significantly impacts the quality and suitability of the finished product. Understanding the properties of different plastics and selecting the most appropriate one for specific applications is essential.
2. Invest in Quality Molds
A well-designed mold can significantly improve the injection molding process. Investing in high-quality molds created by experienced professionals ensures longevity and performance during production.
3. Optimize Machine Settings
Adjusting machine parameters, such as temperature, pressure, and speed, is crucial for producing consistent quality. Regularly monitoring and optimizing these settings can prevent defects and enhance production efficiency.
4. Conduct Regular Maintenance
Maintaining injection molding machines and molds is vital for preventing downtime and ensuring efficiency. A regular maintenance schedule helps extend the life of equipment and maintain high-quality production standards.
Conclusion
The injection plastic mold process stands as a testament to modern manufacturing's progress. Its unmatched efficiency, design versatility, and ability to produce high-quality components make it an invaluable tool for industries across the board. For businesses, especially metal fabricators, embracing injection molding opens up a realm of opportunities for innovation, cost savings, and customer satisfaction. By following best practices and understanding the advantages, companies can position themselves as leaders in their field, meeting the ever-evolving demands of the market.
Ultimately, the marriage of precision engineering and innovative molding techniques represents not just a trend but a fundamental shift in how products are created, assembled, and delivered. This evolution will undoubtedly shape the future of manufacturing, making it a space worth investing in and exploring for anyone in the industry.